FPC
Single layer to 12 layer flex PCB manufacturing service, Accept different stiffener materials: Fr4, PI, Aluminum… Send Your PCB Files to Sales@ucreatepcb.com, we will quote you Very Soon!
FPC is widely used in all kinds of electronic products, according to the number of layers of the board is divided into single-sided, double-sided, multilayer board.
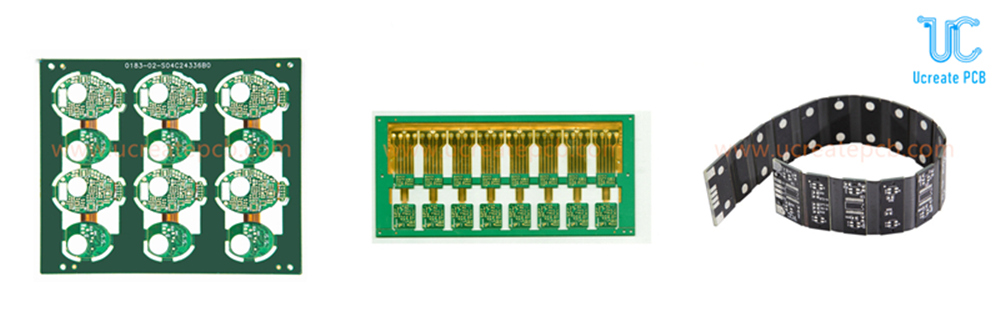
Material Preparation
1. Cutting material
-
Work content: According to the work order size requirements will be formed rolls of material (generally250mm wide) Cut to the required size
-
Main equipment: Automatic unscrambler, Die-cutting machine/automatic film punching machine, Manual cutting machine

2. Baking
-
Work content: Drying the moisture in the substrate, avoid the subsequent production of the impact of rising and shrinking, delamination, etc.
-
Main equipment: Oven
-
Working parameters: Time / temperature
3. Drilling
-
Work content: Drill process holes or pilot holes in the substrate to create conditions for subsequent processes or hole metallization, and also
-
At the same time, it also performs hole processing for various kinds of adhesive and reinforcement plates
-
Main equipment: Drilling machine, auxiliary equipment cutting machine, drill nozzle grinding machine, etc.
-
Working parameters: Feed speed/rotation speed/life time/stack of drilling plates
-
Main defects: Drilling deviation/residual glue/pebble/leakage
4. Electroplating(DMSE)
-
Work content: The DMSE principle is to form nanoscale polymeric conductive substances directly on the PI of the hole wall in place of conventional PTH to create conditions for subsequent copper plating.
-
Main Equipment: DMSE line
-
Working parameters: Temperature / Speed / Time
-
Main defects: Crush pit/cardboard crease
5. Electroplating(Fully copper-plated)
-
Work content: Thicken the hole wall and the copper layer of the face copper to the range required by the work order customer
-
Working principle: The phosphor copper ball placed in the cathode titanium basket continuously precipitates copper ions under the action of acid, which is attracted by the anode flybar and attached to the surface of copper foil to form a copper plating layer, the thickness of the plating layer is proportional to the current density and plating time.
-
Main defects: Uneven thickness of copper / copper particles
6. Dry Film (Pre-treatment)
-
Work content: Cleaning the board, removing oxidation, surface roughening
-
Main treatment method: Micro-etching + pickling
-
Sandblasting (small aperture)
7. Dry film (film application)
-
Work content: A layer of photosensitive dry film is applied to the copper foil surface as the basis for line formation (done in the clean room)
-
Main equipment: STR automatic laminating machine/manual laminating machine
-
Working parameters: Pressure/temperature/transfer speed
8. Dry film (DES-development, etching, de-filming)
-
Work content: Using the work order corresponding to the film exposure, the circuit graphic negative's Image transfer to dry film (done in clean room)
-
Main equipment: RTR exposure machine / semi-automatic exposure machine
-
Quality influencing factors: Copper foil surface cleanliness/light source/exposure time control/negative quality
9.Stacking protective film pre-treatment
-
Work content: Clean the surface, remove oxidation, and increase the bonding force between the overlay film and the substrate
-
Main treatment methods Sandblasting
-
Main equipment:Sandblasting line
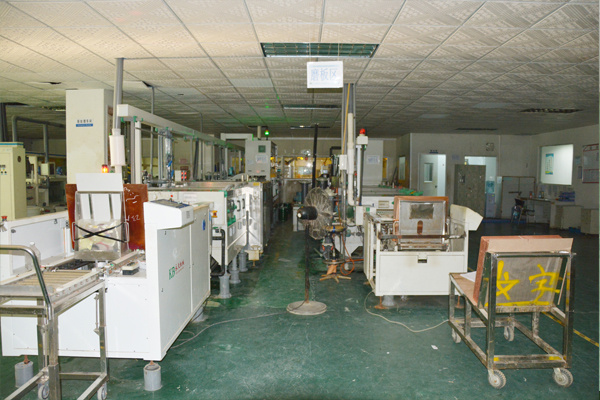
10. Pressed protective film & curing
-
Work content: Through high temperature and high heat pressing and baking to make the covering film or reinforcement and the board between the heat-setting adhesive adhesive curing, so that the two closely combined
-
Main equipment: General quick press / vacuum quick press / oven
-
Main materials: Release film
-
Working parameters: Pressure/temperature/pressing time
-
Main defects: Delamination/uneven flow of glue/pit
11. Target punching
-
Work content: Locate the center of the board graphic according to the light reflection, and use the punch to punch the positioning holes required for the post-process on the FPC.
-
Main equipment: Manual/semi-automatic target punching machine
-
Main defects: Punching off
12. Screen printing (pre-treatment)
-
Work content: Clean the board impurities, remove oxidation, and ensure good bonding between solder resist ink and board surface
-
Main treatment methods: Sandblasting (thin board) / Grinding board + sandblasting
13. Silkscreen Solder Resist Ink
-
Work content: Through the coating or screen printing principle of ink (green oil black oil, etc.) transferred to the product, the screen for part of the ink can be squeezed on the product through the squeegee, other parts are photographic emulsion sealing ink can not leak down, and then through exposure, development, curing to form the intended ink pattern
-
Main equipment: Screen printing machine/exposure machine/developing line/oven
-
Screen printing process: Pre-treatment → Screen printing → Pre-baking → Exposure → Development → Curing
-
Main defects: Foreign matter/imperfect development/losing ink
14. Surface treatment
-
Work content: According to the customer's requirements, using electroplating or chemical principles, the nickel / gold / tin and other metal replacement to the FPC bare pad surface, to protect the pad and maintain its solderability
-
Main Equipment: Ring gold plating line/nickel plated gold line/nickel plated palladium gold line
-
Main surface treatment methods:Gold plating / gold plating / copper tin plating / tin plating / OSP, etc.
-
Major defects: Exposed copper, poor thickness

15. Silkscreen text
-
Work content: Printing the text ink (white oil) onto the product by screen printing principle, mainly printing the product batch number, production week
-
production period, customer requirements of various components labeling, etc.
-
Main Equipment: Screen printing machine/oven
-
Screen printing process: Screen printing of text → curing
-
Main defects: Text blurring/text falling off

16. Assembly reinforcement
-
Work content: Apply the reinforcement to the product by hand/jig/equipment according to the alignment line
-
Main equipment: False paste machine/automatic reinforcement laminating machine
-
Assembly process: Pre-treatment → assembly reinforcement → pressing → curing
-
Reinforcement type and function
PI/FR4 Support
Steel sheet Support/grounding role
Double-sided adhesive for customer assembly
Electromagnetic film Signal shielding
-
Main defects: Offset of reinforcement/foreign material/broken reinforcement
17. Electrical Testing
-
Work content: Through the test jig to detect whether there is open circuit or short circuit between different networks of the board
-
Main equipment: Electrical test machine / flying probe test machine
-
Main defects: Wrinkles/needle marks

18. Molding
-
Work content: Forming customer final product shape by punching die stamping or laser cutting
-
Main equipment: Punching machine / laser cutting machine / gong machine
-
Main forming method: Knife die forming / steel die forming / laser cutting forming
-
Main defects: Wrinkling / punching deviation / dimensional deviation / tearing
19. Finished product inspection
-
Work content: Visual inspection of product appearance and surface condition through manual magnifying glass/equipment, separating good and defective products, and checking whether the product thickness, edge spacing, etc. meet the customer's requirements;
-
Quality sampling inspection of products to further determine whether the product quality meets customer requirements
-
Main equipment: AOI machine/secondary inspection machine
20. Packaging
-
Work content: Packaging according to customer's requirements, ready for shipment into the warehouse
-
Packaging method: Bag/vacuum packing/tray packing/micro-adhesive film packing
Send PCB Files to Sales@ucreatepcb.com, We Will Quote You Very Soon!